next < Page 3, 2, 1 > previous
22 july 2017
I have been in doubt for the Alexandru system. In reality, the planks for the Wales are places on the hull planks. In addition, the yellow and black surfaces run on the side of the hull over the "Wales". By making the 3 rows of "Wales" with 'Ebony" the black and yellow surfaces are divided slightly differently.
As mentioned earlier, I want to make Vic's colors come true by applying various types of wood. I could bring the yellow / black surfaces as they really are, but then I have to put planks together of 2 colors of wood. You already understand ... it becomes very complicated, difficult, etc., in short ... I follow the Alexandru system, which, afterwards, has been considered very well.
The first planks for the lower 'Wale' have been placed. The first plank is always the hardest, because at the same time you need to make some tools to clamp the planks on the hull.
________________
Regards,
Henk
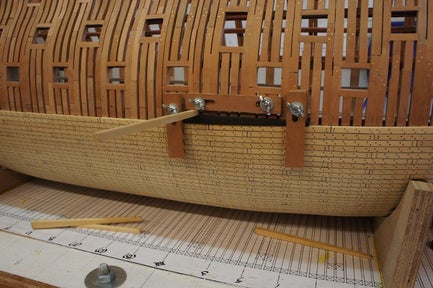
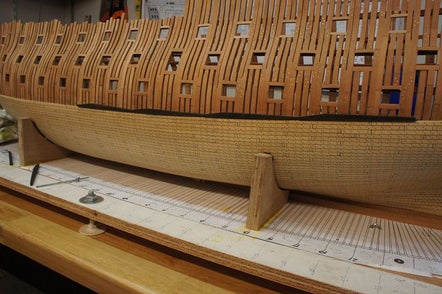
21 july 2017
The planking of the underside hull is ready. Everything just checked out and Vic is right again in her mold.
In addition, I started to set up a part of the workshop for processing copper and brass. I have not already got the copper, but today my new combination machine has come in. With this machine, I can cut, bend and roll plates. As soon as the copper plates come in, I can cut them directly in the small sizse. In addition, I will also make the Brodie of copper and brass, so the machine will be used very well.
________________
Regards,
Henk
16 july 2017
I've been able to work a lot with Vic this week, the front is closed and at the back I have to put around 18 shelves. During the building, the women of the houses regularly look at the result and those visits often lead to small construction meetings.
Thus it is decided not to plan the other side of the hull as intended. There will be a few more shelves and that will be the case. During one of the discussions, the next step is discussed regularly, and so the copper plates are discussed on the hull. The questions were which part, how much and especially how?
Now you can order shaped copper plates where the fasteners are stuck or punch themselves, but in my eyes you miss the small details. If I chose this, I could as well draw the lines and dots on the hull with a nice pencil ;-). So we go for the real details.
The next step is therefore to provide the hull on the tight side with genuine copper plates. This is then in the middle and about a width of about 12 to 15 cm. The plates are made of 0.1 mm thick copper and are made as shown in the picture below. The plates are nailed to the body by the system on the picture (bottom left) with copper nails of 0.3 mm thick and 4 mm long. The cross section of the spherical nail head is approximately 0.9 mm. I ordered only 2500 of them.
Between the planking, I will first make a drill template to provide the copper plates with holes
________________
Regards,
Henk
9 july 2017
The center piece is closed, a few more shelves on the front and then I can close the backside completely. Then turn the mold and close the other side of the hull partially.
Now I regularly get viewers, and although you usually look with the eyes, I agree that the visitor may touch the hull. I have to grind everything with a fine grain if the hull is close and it can not hurt now.
Now yesterday my daughter visited a day and complimented the lines and dots. I had been neatly set up with a nice pencil .... is just real, she said !! That was the second visitor who said to me within one week
Fortunately my wife said at that moment: let's go for a drink of coffee! That was just the salvation of the day.
________________
Regards,
Henk
25 june 2017
The 2nd "Inductive Charging Set - 5V" has come in, so the preparations for the electricity can be closed. The receivers are first fitted with longer cords so that they can walk through the hull
Because the supports of the stand are on section 13 and F, the coils are milled and placed there. The chips and cords are placed a few strings further. Everything is now well below the shelves, still to be fitted. So the steam can be restarted and I can now completely close the hull on the underside.
Planking the hull is not a work that you can do constantly. I have to wait a lot because the glue has to dry or because the curved and stressed wood must dry. That time I use to prepare other things, I have a big list now. Now that the electrical connections have been made to the standard, I can focus on the copper plates and the standard.
Meanwhile, I'm already going to work with the lanterns for the interior lighting. So I have to make about 50 to 60 lanterns, and I can do that soon after all the work. This is still a good job, at least as I want to make it.
________________
Regards,
Henk
22 june 2017
In my previous blogs, I already indicated that I'm going to perform Vic with an Inductive Charging Set - 5V. Now I had little intelligence of electronics, so I called for help from my brother in law Rob. He finally came up with this proposal and got me a large supply of led lamps, cord, etc., ordered.
We would try out everything in a test setup for the first time and could not be put up until last night. The latter was more about me because building in the last few weeks has been delayed by all kinds of causes. Yesterday it was so far and I received further education in the field of electricity, etc.
The charging set thus works with a transmitter that can cordlessly transmit 5 volts. We also want to do it with a USB cable, so we have a printer cable connected to the transmitter. An adapter has also been purchased for the USB connection so that we can also plug it directly into the 230 volt power outlet. After that, the transmitter was measured and we actually had 5 volts on the transmitter.
To see if everything really does, we have 2 LED lights connected to the receiver and I have a 3 mm wooden plate. The receiver is located immediately under the plan, so they are 3 mm apart. Pictures 5 and 6 show that the LED lights start to burn as soon as the receiver reaches the transmitter. Even with a bridge of 10 mm, the lights are still burning.
After all, one charging set can light up about 35 LEDs. For sure, we have bought an additional charging set. In this way, a set is processed in each standard and I can process a total of 70 lamps in the model
On the last picture lies the receiver on the frames. In the coming days, they are milling in the frames, so that he is immediately under the shelter. After that, the shelves are over and then you will see nothing more from the recievers.
________________
Regards,
Henk
2 june 2017
The planking is continuous, another strip of 8 cm, and the closed side is closed. I can not shut him down because I have to make the connection to the electricity.
The latter has come up with a momentum, because I'm going to use something new, that's an inductive link. I do not have all the knowledge about electricity at home and asked my brother-in-law to think about it. Now he is in that industry and he came up with something new to me.
Last time, I indicated that Vic is equipped with lanterns and that I want to let the electrical system work as soon as it is in its new standard. I thought of a kind of click system that would allow 2 contacts to feed the electrical system. Nowadays, you can also do this wirelessly without any kind of contact. This system is called 'Inductive Charging Set - 5V.
One coil feeds the other coil wirelessly as soon as they are opposite each other. The coils feed each other via an inductive coupling and can bridge a distance of 7 to 8 mm. It is therefore the intention that the lower coil will lie under the planing and the other coil in the standard. As a result, approximately 3 mm of each other will lie down.
The system is powered by a 5 volt USB charger, I can also feed the system via the computer. Next week we will make a test setup to see how many LEDs we can feed with 1 coil. We expect about 30 LED lamps of 5 Volt to be able to close to 1 coil, requiring only 1 resistance
Once the test setup is done and we actually know what's possible, I can possibly see if I'm going to build more coils. They are very small and quite cheap, a set costs around € 15.00.
Vic thus becomes the most modern ship as a historic ship. I will post photos of the test setup.
________________
Regards,
Henk
20 may 2017
The planking of the outside is not something to tell something about this blog every week. It's not a boring job, more wood has to be bent and Vic is starting to get more and more impressive. I always try to complete the planing, so bend, place, pen in, grind and polish. That way, I keep the lines well and I do not have to edit anything.
I have been planking the bottom for more than 6 weeks now. The planning is that I will be ready with the planking around 1 August. Meanwhile, I am busy working out other parts. After shaping, part of the trunk is provided with copper plates and I mean real copper.
A few more templates need to be developed and made.
After the summer holidays, Vic will be in a new standard. The ship is equipped with an electrical system that has been completely hidden in the model and will not be visible. The lanterns and other components in the ship will start working by this electrical system. It is intended that this electrical system is automatically powered when Vic is in this standard. This system looks very different from Alexandru's system and is built in a completely different way.
Enough to do so, until over 2 weeks.
________________
Regards,
Henk
7 may 2017
The planking continues steadily, so far everything is on schedule and the lines are well in place. I can work a lot now because a plank can be places anywhere. Yesterday I started the backside at the keel. The plank is wider and needs to be deepened to be beautifully connected.
After all, some wood had to be removed. Then the line of the lower row has been drawn and the first shelf is also applied there. There are 2 more shelves in between and then the entire lower row is ready. Then it's time to draw the lines and place the shelves.
________________
Regards,
Henk
30 april 2017
It took a while, but I'm finally in a good rhythm to bring the shelves and seams. The curves take some extra time because the paper has to be placed in smaller pieces.
________________
Regards,
Henk
23 april 2017
The first top rows are placed. I put Vic back on the mold, because I can better measure the lines on the hull. I took into account the fact that planning with black paper and wooden pens is a lot of work, but, despite having a system now, it takes longer than expected. Planking the middle is quite smooth, but the bow and stern cost more time.
This is because every shelf in this area must be steamed and bent. Especially at the back, there is a fairly sharp angle of almost 90 degrees. The steampan is therefore on display all the time. The profile frame and my adjustable bendmold (with a few solid templates) are widely used. At the moment there is always a shelf to dry on a mold.
Despite all that, it will be fun work to do.
________________
Regards,
Henk
15 april 2017
The first rows of shelves are almost finished, only the bow side and the back must be placed. I decided to quietly take the time to put on the shelves. The result counts. Just drilling and placing pins in the upper rows took two evenings work. Plenty to do so
________________
Regards,
Henk
9 april 2017
This weekend I finally started the real planking of the external hull. First I started with a couple of shelves next to the keel. Uncle Jan gave a hint in the guestbook to get good quality paper and thereby the risk of spots as small as possible. The paper comes to a professional printer from, and is of the best quality, it should therefore not give spots.
The first boards were ready to sanding this morning and it was quite exciting. Will the paper give spots, the contrast is good, etc.? The result is satisfactory, the shelves are beautiful white, the seams are visible and the nuts pins are good.
So I just laid Vic on her side in a couple of pillows and started to make the top shelves under the lowe wale. When sitting on it I can go planking the space between the keel en the top shelves.
Everything here quickly calculated. There must be placed about 560 shelves under the lower wale and there will a total of around 13.440 pins. So we still have some work ahead.
________________
Regards,
Henk